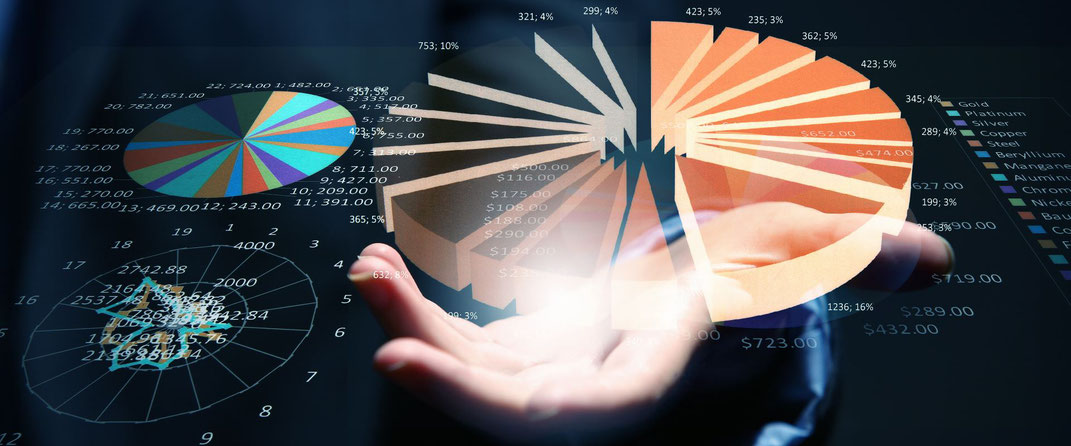
Der Business Case zur Einführung von SAP IBP ist komplex wie bei jedem anderen umfangreichen Softwareprojekt auch. In diesem Beitrag wird kein Template zur Erstellung eines Business Case geliefert. Es sollen stattdessen zwei Aspekte herausgearbeitet werden, die in einem SCM-Planungsprozess und damit auch in einem dafür gedachten Business Case von zentraler Bedeutung sind: Die Auswahl der planbaren und lohnenden Produkte und die Betrachtung des Planungszeitraums in ERP und IBP, um sinnlose Doppelarbeit und inkonsistente Daten zu vermeiden und den Scope eines Business Case und des Projekts präzise zu definieren.
die fünf Kernpunkte des business Case
Allgemein werden in Business Cases zur ERP-Einführung, und analog zur SAP IBP Einführung fast immer die folgenden fünf Kernpunkte genannt:
- Die eigentliche Herausforderung klar benennen, warum eigentlich will man eine Lösung einführen oder ändern?
- Beschreibung des betrachteten Prozesses und insbesondere der Verbesserungspotentiale
- Prüfung der Vorteile, Kosten und Risiken
- Prüfung der Einführungsoptionen
- Der Einführungszeitplan mit Zwischenzielen
Weil all dies schon schwierig genug ist und andererseits vorausgesetzt werden kann, das in jedem Unternehmen die eigenen Mitarbeiter an sich die betriebswirtschaftlichen Fakten am besten kennen konzentrieren wir uns hier auf zwei funktionale Kernthemen:
- Die Auswahl der richtigen Produkte
- Die Definition des richtigen Zeithorizonts für die Teilfunktionen und die Entscheidung wo macht man besser was
Ziel einer Vorauswahl von Produkten und Teilprozessen ist immer die Menge der zu planenden Produkte, Aufträge usw. möglichst klein zu halten. Warum, um dem Planer in ERP oder IBP die Arbeit übersichtlich und wertorientiert zu ermöglichen. Wenn ich mich beispielsweise um 50 Materialnummern kümmern muss, dann ermöglicht das auch die Definition von Arbeitsinhalten, die integrativ die ganze Planungskette umfassen. Besser noch in einem definierten Tages-, Wochen- Monatsrhythmus. Bei 10.000 Materialnummern geht das aus einsehbaren Zeitgründen nicht.
Ziel einer klaren Zuordnung von Planungsfunktionen zu Zeiträumen ist ebenfalls eine Verminderung der Datenmengen, wo immer möglich. Das erleichtert die eigentliche Planung, aber auch die Gestaltung von z.B. Schnittstellen zwischen IBP und ERP. Beispiel ist die Durchführung der Materialbedarfsplanung im Zeitraum der Bedarfe der nächsten sechs Monate. Die Flut an SAP-Stammdaten wie Dispoparameter, Fertigungsversionen, Arbeitsplan, Stückliste, Terminierungsdetails lasse ich besser im MRP und versuche gar nicht erst all das zu replizieren. Die relativ wenigen Stammdaten, die ich für eine optimierte Prognose im IBP brauche, kann ich schnell, richtig und regelmäßig bereitstellen.
Welche Produkte sind eigentlich relevant für SAP IBP?
Welche Produkte sind im Detail wie und wo planbar?
- Produkte, die tatsächlich im IBP geplant werden sollen. Möglichst wenige werthaltige Produkte oder Komponenten, vereinfacht ausgedrückt die A-Teile und wenige B-Teile
- Produkte, Baugruppen, Komponenten, die im ERP-System geplant werden: KANBAN, Bestellpunktartikel, Vendor Managed Inventory usw., vereinfacht ausgedrückt die 90 % der Materialnummern, die technisch notwendig sind, aber weitgehend automatisch oder gar nicht geplant werden.
Ansätze zur Strukturierung der Produktpalette resultieren aus den folgenden Parametern: Umsatz-, bzw. Gewinnbeitrag des Produkts, historische Schwankung der Verkaufsmengen, Art des Produkts unter Planungsgesichtsunkten (Massenfertigung, Kundeneinzelfertigung, Planungsstückliste, Varianten).
Am Beispiel von zwei Produkten soll veranschaulicht werden, wie man die Teilevielfalt in den Griff bekommen kann und damit für SAP IBP plan- und nutzbar macht.
Beispiel 1: Eine gängige Rolltreppe, wie sie zu Tausenden in Bahnhöfen, Flughäfen oder Einkaufszentren genutzt wird besteht aus einigen wenigen Baugruppen wie Fachwerk, Stufen, Motor, Bremse, Schaltkasten usw.
Aufgelöst über die ganze Stückliste kommen aber mehrere Tausend Komponenten zusammen. Will irgendjemand Tausende von Komponenten einzeln planen oder auch nur in einem EXCEL Planungsblatt von IBP sehen? Natürlich nicht.
Im ersten Ansatz ergibt sich, dass ein Montageband dieser Rolltreppen aus 8 Fertigungsschritten besteht und jeder einige Stunden benötigt. Daraus resultiert eine Fertigungskapazität von max. 4 Fahrtreppen am Tag / Band und Schicht. Da bleibt eigentlich nicht so viel zu planen. Interessanter wird es bei Betrachtung der unterschiedlichen Modelle. 3 unterschiedliche Basismodelle ergeben unterschiedliche Auslegung von Baugruppen und womöglich unterschiedliche Motoren, Bremsen usw. Aber selbst dieser Grad an Detail ist für die Lieferanten im Zweifel eher unwichtig. Denn für die Lieferanten ist es wichtiger wenige Tage vor Montageanlieferung im Detail zu wissen welcher Motor, welcher Schaltkasten usw. zu liefern ist und sie liefern gemäß Terminvereinbarung und Spezifikation. Das heißt sie benötigen detaillierte Fertigungsunterlagen und eingespielte Bestellprozesse, aber das ändert wenig an der Menge von z.B. 8 Stück / Tag. Genau betrachtet gibt es nur ca. 30 auftragsabhängige Baugruppen oder Komponenten pro Montageauftrag.
Es stellen sich jetzt 2 weitere Fragen, wie werden die erwähnten Tausende von Komponenten an die Montagelinie gebracht und bleibt überhaupt noch irgendetwas außerhalb der Materialbedarfs-planung langfristig zu planen?
Antwort zur ersten Frage; wie in fast jeder Montagelinie gibt es tausende, in diesem Fall ca. 1000, Komponenten, die in der Tat überhaupt nicht geplant werden und über Vendor Managed Inventory behandelt werden. Einige weitere Hundert kommen über Umlagerungs-KANBAN oder direkt Einkauf-KANBAN an die Linie. Die Umlagerungs-KANBAN werden im zweiten Schritt über Bestellpunkt-verfahren im MRP nachbestellt.
Antwort zur zweiten Frage; einige sehr kritische planungsrelevante Teile bleiben relevant für z.B. die langfristige Absatzplanung in einer nur auf den ersten Blick überraschenden Materialgruppe, die Ersatzteile. Diese Erkenntnis gewinnt nicht nur der Reisende, der vor einer stehengebliebenen Treppe steht. Ersatzteile können und sollen separat geplant werden. Denn Ersatzteile sollen nicht für die bekannten Probleme, wie z.B. Teile-Kannibalismus zwischen OEM- und After Sales Geschäft sorgen. Und Ersatzteile sollten möglichst dicht am Ort verfügbar sein, wo sie benötigt werden. Mit anderen Worten: Im Industrieumfeld gibt es eine hohe Anzahl von Branchen, in denen Ersatzteile ein lohnendes Umfeld bezüglich Absatzprognose (OEM plus After Sales), räumlicher Verteilung (Netzwerkplanung) und Lieferfähigkeit (räumlich verteilte Zielbestände) bilden. Genau die 3 Kernthemen von SAP IBP.
So bleibt häufig eine aus SAP IBP-Sicht lohnende Produktgruppe unentdeckt. Die den zusätzlichen Vorteil hat mit gängigen Prognosemodellen sehr gut abbildbar zu sein und für den Planer in der Regel mit einer übersichtlichen Anzahl von Materialnummern zu bearbeiten ist.
Mögliches Ergebnis der Produktauswahl in diesem Beispiel:
- 3 Standardvarianten der Basismodelle ausgeplant über >= 1 Jahr und mit ständiger monatlicher Anpassung
- Einige Hundert Ersatzteile und Baugruppen
Beispiel 2: Variantenreiche Produkte, wie z.B. Druckminderer lohnen fast immer einen genauen Blick in jedem Fall. So unterscheiden sich z.B. Druckminderer, wie sie zu Tausenden in Laboren verwendet werden häufig nur in ihrem zu regelnden Druckbereich (in Stufen von 0,x bis 300 bar) und der gasspezifischen Farbkennzeichnung. Der Druckbereich wird über eine druckbelastete Feder und die Farbkennzeichnung mit billigen Plastikplatten unterschieden. Anders ausgedrückt x Druckbereiche mal y Gase ergeben Dutzende Materialnummern im Detail, aber genau genommen nur ein planrelevantes Produkt, das z.B. mit einer Planstückliste abgebildet werden kann. Feder und Plastikkappe als C-Artikel sind klassische KANBAN- oder VMI-Teile.
Das heißt, eine Betrachtung der einzelnen Materialnummer mit stark schwankenden, bzw. kleinen Verkaufsmengen führt zum womöglich falschen Ergebnis, das eine langfristige Planung schwer oder statistisch unmöglich ist. Fasst man den ganzen Variantenreichtum einer solchen Gruppe zusammen, dann kommt man zu einem ganz anderen Ergebnis
Und wie im Beispiel 1 gibt es auch bei Variantenprodukten viele Branchen mit ähnlichen Planungsproblemen.
Zur Auflösung einer solchen Plan-Produktgruppe bieten sich in IBP und ERP mindestens 2 Möglichkeiten (mehr dazu im Beitrag über die Materialbedarfsplanung)
Mögliches Ergebnis der Produktauswahl in diesem Beispiel:
- Jeweils 1 Standardvarianten der Basismodelle ausgeplant über >= 1 Jahr und mit ständiger monatlicher Anpassung, eventuell Merkmalsverteilung über das Merkmal Gas
- Einige Dutzend Ersatzteile und Baugruppen
Schlussfolgerung und Warnung vor einem logischen Dilemma
Es gibt im Wesentlichen drei Gründe, bzw. Einflüsse für eine klare Definition der im IBP (oder allgemein in einem externen Planungssystem) geplanten Produkte:
a) Die Stücklistenkomplexität
Die Komplexität hängt vereinfacht gesagt auch von der Branche ab. Maschinenbau, Anlagenbau, Elektrotechnik haben eher komplex-mehrstufige Stücklisten mit mehreren werthaltigen Baugruppen. Chemie, Massenserienfertigung, viele Konsumgüter, Textilien sind eher einfach aufgebaut. Das Planungsdilemma liegt hier in der Frage, ob als IBP-Planungsergebnis ein Planprimärbedarf oder ein Planauftrag ins ERP-System zurückgespielt wird. Ohne hier ins Detail gehen zu können ist bei sehr komplexen Stücklisten eher der Ansatz Primärbedarf zu sehen, bei einfachen Stücklisten eher der Ansatz Planauftrag (bzw. es ist vielleicht sogar egal). Das hat dann auch eine direkte Auswirkung auf die Nutzung von IBP-Funktionen. Wenn die Netzwerkplanung genutzt wird, dann wird häufig davon ausgegangen, dass Planaufträge entstehen. Diese Prämisse ist akzeptabel, aber mit der Einschränkung, dass sich dies auf einfache Stücklistenstrukturen bzw. Produkte bezieht.
b) Rhythmus der Planung
In der Nutzung von IBP oder APO wird häufig ein monatlicher Prozess mit teils wöchentlichen Updates vorgeschlagen und auch praktiziert. In Fortführung der Gedanken zur Stücklistenkomplexität ist ein einmonatlicher Planungsprozess auch angemessen, denn die vielfältigen Störungen im Praxisbetrieb müssen meist schnell behoben werden und das passiert dann auch besser im ERP-system direkt. Und zur Verminderung von verwirrenden und inkonsistenten Planungssituationen auf unteren Stücklistenstufen und Verfügbarkeits-ergebnissen auf der obersten Produktebene ist die Nutzung von Planaufträgen als Ergebnis für das ERP-System nur bei einfach aufgebauten Produkten zu empfehlen
c) Bedienbarkeit und Stammdatenpflege
Dies ist an sich selbsterklärend. Es ist nichts für den Planer gewonnen in IBP mit Tausenden von Materialnummern umzugehen. SAP selbst hat im ERP-System mit Funktionen wie MRP live die besseren Werkzeuge, die zudem den Vorteil haben in Real Time auf Änderungen operativ zu reagieren.
Ein Unternehmensplanungssystem wie SAP IBP beschränkt sich dann auch auf die wesentlichen Produkte und Attribute. Fehler und Abweichungen sind hier eher über Dashboards, Alerts und KPI zu verfolgen, die ein Eingreifen dann auf den Ausnahmefall einschränken.
In welchem Schritt der Prozesskette wird für welchen Zeitraum geplant?
Die wesentlichen Funktionen der Planungsprozesskette im SAP IBP als auch im ERP-System lassen sich relativ einfach einem bestimmten Zeitraum zuordnen, für den die Daten ausgewertet und ermittelt werden.
Einschränkung: Alle hier gezeigten Ausführungen hängen für den tatsächlichen Planungszeitraum zu einem großen Teil von der Wiederbeschaffungszeit, bzw. von der Durchlaufzeit bei Eigenfertigung ab. Diese Werte sind je nach Produkt und Lieferantenbeziehung stark schwankend im Bereich von wenigen Tagen oder Wochen bis zu mehr als einem halben Jahr. Die hier gezeigten Schätzungen beziehen sich auf Produkte mit einer Gesamtbeschaffungszeit von 3 – 6 Monaten.
Das hat einige plausible Gründe:
a) Nicht in jedem Fall, aber sehr oft, hat man in einem ERP-System Zehntausende aktive Materialnummern, die alle im MRP-Lauf planungsrelevant sein können. Aus oben genannten Gründen macht es wenig Sinn diese Datenmenge im relevanten Zeitraum bis zu 6 Monaten (plus/minus je nach Gesamtbeschaffungszeit) in ein Planungssystem wie SAP IBP oder auch SAP APO zu replizieren.
b) Nach 2 Jahrzehnten des Stillstands im SAP ERP bis genau gesagt SAP ECC EHP6 musste für eine detaillierte Terminierung der Eigenfertigung entweder APO PP-DS oder die etwas schwierig handhabbare Plantafel im ECC verwendet werden. In jedem Fall ein Zusatzaufwand und trotzdem nicht einfach. Ab SAP ECC EHP 7 oder SAP S/4 HANA ändert sich der Prozess grundlegend, denn PP-DS ist integriert im ERP-system verfügbar. Im Ergebnis hat das Unternehmen nicht nur eine komplette MRP-Planung, sondern auch noch optimierte Termine der Eigenfertigung im kurzfristigen Horizont.
c) In der Materialbedarfsplanung selbst gibt es nicht ohne Grund einen Fixierungshorizont für die einzelnen Materialnummern, der sich mindestens aus der Durchlaufzeit der Eigenfertigung oder auch einem Anteil der Planlieferzeit ergibt. Denn jede dispositive Änderung im operativen Bereich am Endprodukt sorgt für eine Flut von Änderungen in der Stücklistenstruktur.
So ergibt sich als Anhaltspunkt für den Business Case und die Lastverteilung zwischen ERP und IBP folgende Funktionsverteilung
• - 2 Jahre bis heute Istdaten Umsatz, Lieferung
o Basis für Prognose in IBP for Demand
o Basis für Prognose in ERP für alle nicht im IBP geplanten Materialnummern
• - 3 Monate bis + 3 Monate Istdaten Umsatz, Lieferung, historische Prognosewerte
o Basis für kurzfristige Prognosekorrektur in IBP for Demand
• Heute bis + 3 Monate
o Basis für PP-DS als Folgeprozess nach MRP in ERP
• Heute bis + 3 – 12 Monate Bedarfsplanung Kundenbedarfe, Planprimärbedarfe
o Basis für Materialbedarfsplanung in ERP MRP, auch in Kopplung mit PP-DS
o Stark schwankend und stark abhängig von der Gesamtwiederbeschaffungszeit
• + 3 Monate bis 12 – 24 Monate Plandaten in SAP IBP
o Absatzplan in IBP for Demand und damit der Planprimärbedarfe im ERP-System
o Ziel- und Sicherheitsbestand in IBP IO und damit der Zielbestände im ERP-System
o Restriktionsgeprüfter Liefer- und Netzwerkplan als Grundlage für werksverteilte Planprimärbedarfe im ERP
o Kapazitäten in Fertigung und bei Lieferanten in IBP for Supply als optimierte Basis für die Pflege des Kapazitätsangebot im ERP-System und Kontrakte mit Lieferanten. Diese Pflege erfolgt in der Regel durch manuelle Stammdatenpflege.
• 3 Monate bis 2 Jahre in der Zukunft
o Regelmäßige Definition und Anpassung des Absatzplans in SAP IBP
o Regelmäßige Definition und Anpassung von Kapazitätsbedarfen und Bestandsvorgaben in der Netzwerkplanung und Bestandsoptimierung im SAP IBP
SAP schlägt für die ständige Anpassung der Plandaten dezidierte Termine in einem festen Rhythmus über einen Zeitraum von 1 Monat vor, in denen mit geeigneten Werkzeugen (Kollaboration mit JAM) in IBP die beteiligten Planer und Analysewerkzeugen (Reports, KPI und Alerts) in IBP die Plandaten ständig gemeinsam überprüft und bestätigt werden. Mehr zu diesem Thema der Prozessdefinition im Beitrag über die Netzwerkplanung in dieser Serie.
DER Nutzen des richtigen Planungsansatzes
Die Vorteile, die sich aus dieser Material- und Softwarevorauswahl ergeben sind unmittelbar einsichtig.
- Die Menge und damit auch der Zeitaufwand der zu planenden Materialmengen werden überschaubar.
- Es sollte eigentlich keine Doppelbearbeitung von Plandaten in ERP und Planungssystem geben, damit werden von vornherein Inkonsistenzen vermieden
- Eventuell auftauchende Schnittstellenfehler sind schneller identifizierbar und korrigierbar und Timeouts in der Schnittstelle sollte es so auch nicht geben.