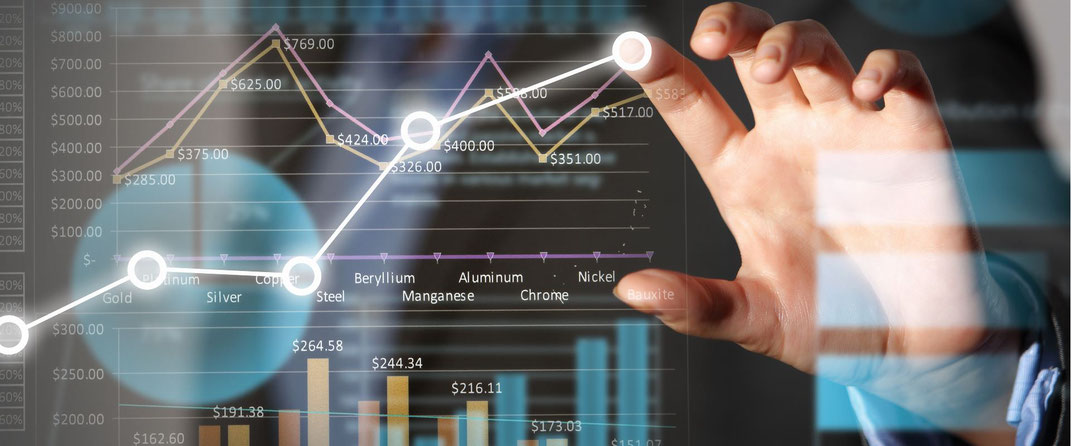
Der Kundenbedarf aus planerischer Sicht. Dabei geht es im Wesentlichen um folgende drei Fragen:
Welche Planstrategie wird einem Kundenbedarf zugeordnet, was mache ich eigentlich mit diesem Bedarf im Planungsprozess?
Wie kann der Kundenbedarf (Menge und Termin) bestätigt werden bzw. welche Möglichkeiten der Verfügbarkeitsprüfung hat man?
Was ist eigentlich der Zusammenhang zwischen Planungsstrategie, Verfügbarkeitsprüfung und Servicelevel?
SAP stellt im ERP seit R/2-Zeiten sieben Basisstrategien zur Verfügung, die einem Kundenbedarf zugeordnet werden können. Einige dieser Strategien setzen sogenannte Planprimärbedarfe voraus. Die Planung dieser Planprimärbedarfe wird im nächsten Beitrag dieser Serie im Detail besprochen. Es ist hier ein wenig wie mit dem altbekannten Henne-Ei Dilemma. Kommt der reale Kundenbedarf zuerst oder der geplante Kundenbedarf (Planprimärbedarf). Die sieben Strategien bestimmen, ob ein Kundenbedarf mit einem Planprimärbedarf verrechnet wird und wie.
Die Verfügbarkeitsprüfung im ERP arbeitet an sich immer in zwei Schritten:
Gibt es einen ausreichenden Bestand zum Kundenbedarf zum gewünschten Termin im gewünschten Auslieferungswerk? Wenn ja, wird dieser Termin bestätigt. Wenn nein, wird anhand der bereits vorhandenen Zugänge (Fertigung, Einkauf, Planprimärbedarf) geprüft, wann dies der Fall ist. Notfalls wird ein Kundenbedarf in mehrere Teilmengen gesplittet und entsprechend bestätigt.
Der Servicelevel ist erst einmal eine Kennzahl (Key Performance Indicator / KPI) und kann vereinfacht in mindestens drei Varianten gemessen werden. Sofortige Lieferfähigkeit der gewünschten Kundenbedarfe in Prozent; Lieferfähigkeit zum gewünschten Termin des Kundenbedarfs; tatsächliche Lieferung zum gewünschten Termin des Kundenbedarfs. Mindestens ein KPI wird üblicherweise gemessen: Die Lieferfähigkeit zum gewünschten Termin. An sich empfiehlt sich, alle drei KPI mindestens täglich zu messen. Und anhand der KPI-Definition ergibt sich unmittelbar die Abhängigkeit des Ergebnisses von Bestand und / oder Planbedarf (Planzugang) als Relation zum Kundenbedarf. Anders ausgedrückt, jede Bemühung der Bestandsoptimierung und der Absatzplanverbesserung verbessert unmittelbar den Servicelevel.
Welche Planungsstrategien gibt es und was bedeuten diese für die Lieferfähigkeit?
Angeboten werden von SAP sieben Basisstrategien zur Planung bzw. zur Verrechnung von Kundenbedarfen gegen vorher ermittelte und hinterlegte Planprimärbedarfe. Wenn z. B. die Strategie 40 ‚Vorplanung mit Endmontage‘ für ein Produkt gewählt wurde und 100 Stück im Monat Mai 2020 geplant sind, dann wird vereinfacht die Beschaffung angestoßen, um 100 Stück im Mai 2020 auf das Lager zu legen. Gibt es nun einen Kundenwunsch von 55 Stück im Mai 2020, dann werden vom Planprimärbedarf 55 Stück abgezogen und als Basis für die Materialbedarfsplanung gibt es dann im Ergebnis zwei Primärbedarfe: 55 ST aus dem Kundenauftrag und Rest 45 ST Planprimärbedarf. Entscheidend ist, dass die Summe erst einmal bei 100 ST im Mai 2020 bleibt.
Anonyme Lagerfertigung
Kundeneinzelfertigung
Losfertigung
Vorplanung mit Endmontage
Vorplanung ohne Endmontage
Vorplanung mit Vorplanungsmaterial
Vorplanung der Baugruppen
Verkauf ab Lager ohne Abbau von Planprimärbedarf durch Kundenauftrag.
Einzelner Kundenauftrag ohne Verrechnung und ohne Lagerbestand.
In Losfertigung gefertigter Kundenauftrag.
Kundenauftrag mit Verrechnung Planprimärbedarfe.
Kundenauftrag mit Verrechnung Planprimärbedarfe, Montagefertigung wird durch Kundenauftrag ausgelöst. Diese Strategie empfiehlt sich als Verbesserung der Kundeneinzelstrategie.
Kundenauftrag mit Verrechnung gegen einzelne Materialnummern, die nicht auf Endproduktebene disponiert werden, aber für viele Endprodukte genutzt werden und separat geplant werden können (z.B. teure Rohstoffe).
Kundenauftrag mit Verrechnung gegen Baugruppen, die nicht auf Endproduktebene disponiert werden, aber für viele Endprodukte genutzt werden und separat geplant werden können. Als Abwandlung kann dies auch eine Baugruppe ohne Montage sein.
Einige dieser sieben Grundstrategien haben leicht abgewandelte Details, so dass bei der Einstellung im ERP-System von SAP ca. 20 Basisstrategien angeboten werden.
Zwei Ergebnisse einer Vorplanung mit Planprimärbedarfen gibt es immer:
- Die Beschaffung von Produkten und Komponenten kann ohne Kundenauftrag, immer in Abhängigkeit von Beschaffungszeiten angestoßen werden.
- Tatsächliche Kundenbedarfe können auch ohne Lagerbestand zum Termin bestätigt werden.
Das mag erst einmal für viele Experten trivial klingen, die unbeantwortete Frage ist, warum gibt es dann so viele Unternehmen, in denen der Lieferservice trotzdem schlecht ist. Drei Gründe fallen dem erfahrenen Planer quer durch alle Unternehmen häufig auf:
DREI GRÜNDE FÜR SCHLECHTEN LIEFERSERVICE
- Die Gesamtbeschaffungszeit der Endprodukte ist schlicht zu lang, um sinnvoll in irgendwelchen weit in der Zukunft liegenden Perioden zu planen. Hier hilft ERP oder Planungssoftware wenig bis nichts, dies ist eine integrierte Daueraufgabe von Entwicklung (Modularisierung, Gleichteile usw.), Arbeitsplanung (integrierte Arbeitsvorgänge, j.i.t. Montage usw.) und strategischem Einkauf (VMI, Fremd-KANBAN, Lieferzeiten usw.). Ziel ist immer eine möglichst kleine Wiederbeschaffungszeit der Endprodukte zu realisieren.
- Es gibt im Unternehmen keine oder falsch geplante Planprimärbedarfe, so dass im Ergebnis die Bestätigung von Kundenbedarfen häufig einem Blick in die Kristallkugel gleicht.
- Das Instrumentarium der oben gezeigten Planstrategien wird nicht verstanden und viele Produkte haben die falsche oder keine Strategie zugeordnet, was im Ergebnis den vorigen Punkt verstärkt, bzw. im MRP-Lauf zu falschen Ergebnissen führen muss.
Und hier schließt sich der Kreis; im nächsten Artikel dieser Serie wird es genau darum gehen, wie die Absatzplanung und die daraus resultierenden Planprimärbedarfe in SAP IBP besser durchgeführt werden können als im ERP-System. Und wie im vorigen Blog-Artikel für den Business Case gezeigt, sind die besonders ‚wertvollen‘ Produkte für die Planung identifiziert, dann muss im zweiten Schritt jedem einzelnen die richtige Planungsstrategie zugeordnet werden.
Ein Tipp: Lassen Sie sich einmal von ihren Disponenten Planungsstrategien und die korrespondierenden Daten im SAP-Materialstamm erklären. Nicht immer, aber oft, werden Sie einen spontanen Ansatz für ein Projekt zur Verbesserung der Planung finden.
Möglichkeiten zur Verbesserung der Verfügbarkeitsprüfung (ATP-check)
DIE VIER ELEMENTE DER VERFÜGBARKEITSPRÜFUNG
Die Verfügbarkeitsprüfung kann unabhängig von Software an sich nur vier Elemente prüfen:
- Vorhandenen Bestand im vorgesehen Lieferwerk – bereits zugesagte Mengen für vorhandene Kundenaufträge: Dies ist der Standardfall der SAP-ERP Prüfung und muss hier nicht weiter betrachtet werden.
- Vorhandener Bestand in einem alternativen Lieferwerk – bereits zugesagte Mengen für vorhandene Kundenaufträge: Dies kann manuell in SAP ECC geprüft werden und wird in SAP S/4 HANA in der Einstellung vereinfacht und verbessert. Schwierig wird es in SAP ECC, wenn genau dies oft vorkommt; dann bleibt bisher der sogenannte gATP ‚global ATP check‘ mit Hilfe von SAP APO oder Programmierung.
- Zukünftiger Bestand im vorgesehen Lieferwerk – bereits zugesagte Mengen für vorhandene Kundenaufträge: Dies ist der Standardfall der SAP-ERP Prüfung und muss hier nicht weiter betrachtet werden.
- Zukünftiger Bestand in einem alternativen Lieferwerk – bereits zugesagte Mengen für vorhandene Kundenaufträge: Dies kann manuell in SAP ECC geprüft werden und wird in SAP S/4 HANA in der Einstellung vereinfacht und verbessert. Schwierig wird es in SAP ECC, wenn genau dies oft vorkommt; dann bleibt bisher der sogenannte gATP ‚global ATP check‘ mit Hilfe von SAP APO oder Programmierung.
Als Verfeinerung sollen hier noch 2 gebräuchliche Varianten dargestellt werden:
Die Kontingentierung segmentiert den aktuellen und den zukünftigen Bestand und allokiert definierte Mengen einzelnen Kunden oder Gruppen. Die Kontingentierung, bzw. Allokation ist insbesondere im Handel gebräuchlich (z.B. für die Verteilung einer beschränkten Menge auf möglichst viele Geschäfte). Die Nutzung ist auch im SAP ECC möglich (dort aber wegen schlechter Bedienbarkeit nicht sehr gebräuchlich) und wird voraussichtlich durch eine Verbesserung in SAP S/4 eine weitere Verbreitung finden.
Im Zusammenspiel mit dem APO, bzw. dem zukünftigen S/4 Modul PP-DS, ist noch Capable-to-Promise zu erwähnen, in der ein simulierter Planauftrag direkt auf Machbarkeit geprüft wird, und dann direkt terminiert im Kundenauftrag zum Termin bestätigt werden kann. Eine Funktion, die in der Zukunft viele Nutzer von Variantenkonfiguration in Zusammenhang mit dem embedded PP-DS im S/4 erfreuen sollte.
ANSÄTZE ZUR VERBESSERUNG DER VERFÜGBARKEITSPRÜFUNG
Wirklich befriedigend ist das für viele Kunden, insbesondere bei Bestand eines Produkts in mehreren Werken (Lägern) und einer Nutzung des Standards ohne Programmiererweiterungen, nicht.
Drei Ansätze zur Verbesserung sind darstellbar in der Mehrwerksituation mit unterschiedlicher Komplexität.
- Technisch sauberer ATP check in mehreren Werken. Ohne S/4 HANA und APO bleibt hier wirklich im ECC nur die Programmierung. Mit S/4 HANA ist das technische Problem mit Glück auf eine Aufgabe im SAP-Customizing reduziert, bei komplizierten Lieferketten kann weiterhin Programmierung notwendig sein.
- Nutzung kapazitätsoptimierter Terminierung bei Eigenfertigung (egal ob Plan- oder Fertigungsauftrag). In diesem Fall stimmen wenigstens die ATP Ergebnisse im geprüften Werk bezüglich des Zeitpunkts einer Kundenbestätigung. Diese Funktion steht auch ECC-Nutzern zur Verfügung, allerdings mit bekannten Einschränkungen in der Bedienbarkeit. Sinnvoll ist hier in jedem Fall die Prüfung, ob PP-DS als Funktion im Zeitraum bis 6 Monate im Unternehmen praktikabel einsetzbar ist, eine optimale Terminierung zu ermöglichen.
- Planung der Primärbedarfe in SAP IBP for Demand und / oder Netzwerkplanung verbessert das Problem an der Wurzel, nämlich dadurch, dass die bestmögliche Planmenge in der bestmöglichen Verteilung über Werke und Läger die Basis des ATP-Checks darstellt.
Und mit dem letzten Punkt kann auf die drei folgenden Artikel, sozusagen das Herzstück der Serie zur Absatzplanung (richtige Planmenge), zur Bestandsoptimierung (richtiger Planbestand am richtigen Ort) und zur Netzwerkplanung (optimiertes Lieferangebot, um die Planmenge am richtigen Ort zur Verfügung zu stellen), verwiesen werden.
Im Ergebnis bedeutet das, der ATP check als solcher findet nach wie vor im ERP-System statt mit den erwähnten Schwierigkeiten. IBP hilft hier indirekt, wenn tatsächlich im Unternehmen ein kompletter und optimierter Absatzplan zur Verfügung gestellt wird, und der kann eigentlich nur aus einem externen System wie SAP IBP kommen. Wenn er aber vorhanden ist, dann verbessert sich oft die Situation aus Kundensicht und aus MRP-Sicht schlagartig. Ein erfolgreicher ATP-Check zum Kundenbedarf ist immer auch ein ‚Bonuspunkt‘ im Servicelevel. Die Voraussetzungen zur Verbesserung des Servicelevel sind, wenig überraschend, eine gute Bestands- und Absatzplanung, also genau die beiden traditionellen Bausteine, die dem Planer ohne und mit SAP IBP zur Verfügung stehen.
VORTEILE AUS PLANUNGSSTRATEGIE UND OPTIMIERTEM ATP-CHECK
Die Vorteile, die sich aus der richtigen Planstrategie und einem optimierten ATP-Check ergeben sich unmittelbar
- Die bestätigten Mengen und Zeitpunkte sind deutlich korrekter als bisher und vermeiden falsche Kundenzusagen und damit Unzufriedenheit beim Kunden.
- Fehlende Mengen sind schneller identifizierbar und ermöglichen eine verbesserte Kommunikation mit dem Kunden zur Vereinbarung bestmöglicher Alternativen, wenn es wirklich nicht wunschgemäß geht.
Sie möchten mehr erfahren, wie Sie Ihre Verfügbarkeitsprüfung im Zusammenspiel mit IBP optimieren können?
Kontaktieren Sie uns für einen kostenlosen IBP-Workshop mit Systemdemo und Abgleich Ihrer Anforderungen!